Formación de espuma
Termoplàsticos > ► Polímeros espumados
Teoría de la formación de espuma
Estructura de las espumas
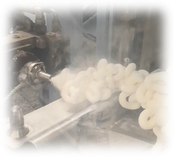
Efecto de la formación de espuma en las propiedades
Las propiedades de las espumas plásticas vienen dictadas por las propiedades del material pero también por las propiedades de sus células, más claramente la estructura de las células. Los diferentes materiales con diferentes densidades aparentes y celulares no se pueden comparar directamente, pero se pueden hacer generalizaciones. Dado que el enfoque de la tesis está en las propiedades mecánicas, no se discutirán otras propiedades como el aislamiento térmico o acústico. La formación de espuma a menudo deteriora las propiedades de tracción del material. Esto se debe a la menor densidad del material. Wong y col. estudiaron los efectos de los parámetros de procesamiento sobre la estructura de la espuma y las propiedades mecánicas durante la microespuma de TPO. Descubrieron que la densidad relativa disminuida provoca una resistencia a la tracción disminuida pero un alargamiento aumentado. Para el módulo de tracción, el efecto no fue tan sencillo, pero a medida que la densidad disminuyó, el módulo de tracción comenzó a disminuir hasta que volvió a aumentar después de alcanzar una densidad relativa de 0,9. Cuando se espuman materiales flexibles, incluidos los TPE, se ha descubierto que un mayor tamaño de celda reduce la dureza. Nema y col. encontraron que cuando se formaba espuma químicamente, la dureza del TPU disminuía de 85 a 55 ShA con una reducción de densidad del 34%. Se desearía una caída similar para las juntas. Los defectos superficiales casi siempre ocurren durante la formación de espuma. Normalmente son causadas por la formación de células prematuras y pueden verse afectadas por el ajuste de los parámetros de procesamiento. Las rayas de tigre son los defectos más comunes que se encuentran en los termoplásticos. No solo son un problema con la formación de espuma, sino también con los sólidos, por ejemplo, mezclas de PP / caucho / talco. Son franjas de diferentes grados de brillo o brillo, que aparecen perpendiculares a la dirección del flujo. Guo y col. descubrió que cuando se formaban químicamente espumantes TPO, en lugar de rayas de tigre, se encontraban rayas plateadas. Además de ajustar los parámetros de procesamiento, se encontró que el uso de PP ramificado en lugar de piezas lineales producidas con menos defectos.
Métodos de formación de espuma
La formación de espuma se realiza principalmente mediante espumación química, física o sintáctica. Los métodos químicos y físicos se basan en agentes de soplado (BA), que son medios para liberar gas en el sistema. Estos métodos crean células que tienen paredes del polímero matriz. La formación de espuma sintáctica se basa en esferas separadas llenas de gas, generalmente polímero de vidrio, que se mezclan con el material. Algunas esferas de polímero pueden expandirse a medida que las condiciones térmicas se vuelven adecuadas durante el procesamiento, creando esferas con paredes muy delgadas. Se denominan microesferas expandibles y son la única forma de formación de espuma sintáctica discutida en la tesis.
Espumación física
Los agentes espumantes físicos (PBA, también agentes espumantes físicos PFA), forman gas al experimentar un cambio en el estado físico. Suelen ser gases inertes, que se disuelven en el polímero en estado fundido, o líquidos que tienen un punto de ebullición bajo. Además, se utilizan PBA sólidos, pero solo para termoendurecibles y cauchos. Es crucial para una espumación exitosa que el PBA se disuelva completamente en el polímero fundido. La disolución depende de la solubilidad del agente de expansión, la presión de saturación, el grado de mezcla y el tiempo de residencia.
Gas como agente de soplado físico
El uso de gas como PBA en la formación de espuma se basa en la difusión. El material se satura primero con gas a alta presión, y cuando la presión se reduce, el gas se difunde fuera del material de la matriz y se forma espuma. Los gases utilizados de esta manera incluyen nitrógeno (N2), dióxido de carbono (CO2), butano, hidrógeno, helio y muchos otros, pero se utilizan principalmente N2 y CO2. El dióxido de carbono es el BA más utilizado, si se considera su uso en todos sus estados. Es barato, seguro de usar, abundante y seguro para el medio ambiente, aunque es un gas de efecto invernadero. También tiene una alta solubilidad a los polímeros fundidos, lo que permite una alta saturación a bajas presiones, pero ralentiza la tasa de caída de presión. Esto hace que las células se expandan durante demasiado tiempo y que el tamaño de las células sea más difícil de mantener pequeño. El problema surge principalmente en la formación de espuma de productos de gran tamaño. También contribuyen al amplio uso la temperatura y la presión críticas, que son necesarias para lograr un fluido supercrítico utilizado en la fabricación de espumas microcelulares o de baja densidad. Para el CO2, estos valores son 31°C y 7,38 MPa, mientras que para el N2 son -146,9°C y 3,4 MPa, respectivamente. El nitrógeno tiene algunas de las mismas ventajas que el CO2. Es seguro de usar, barato y abundante, sin mencionar que es seguro para el medio ambiente, ya que simplemente se toma prestado de la atmósfera. Además tiene algunas ventajas en comparación con el dióxido de carbono. Si se estudian espumas con el mismo porcentaje en peso de PBA, se encuentra que con N2 se ha logrado una mayor densidad celular y relación de expansión. Los productos espumados de N2 también se encogen menos, ya que es el componente principal en la atmósfera y la difusión dentro y fuera del material es casi igual. La desventaja es que el N2 tiene baja solubilidad en polímeros fundidos y, debido a esto, su uso se limita principalmente a la microespuma. Los sólidos no son exactamente PBA, sino más bien absorbentes de PBA. El sólido se satura primero con gas o líquido de bajo punto de ebullición a presión y durante la formación de espuma se inicia la nucleación al aumentar la temperatura. Los gases usados de esta manera incluyen cloruro de metileno, cloramina y acetona, mientras que se pueden usar la mayoría de los líquidos mencionados anteriormente. El material sólido puede ser carbón, arcilla o gel de sílice, entre otros. Los sólidos solo se utilizan para termoestables y cauchos, y para la producción de caucho tienen una ventaja en comparación con otros. El uso de carbón ultramicroporoso saturado con CO2 asegura la formación de espuma en condiciones de vulcanización. En el lado negativo, con el método solo se pueden lograr espumas de alta densidad con estructuras celulares heterogéneas.
Agentes nucleantes
Los agentes nucleantes se utilizan con PBA para mejorar la nucleación celular homogénea. Esto significa una distribución de tamaño de celda estrecha y una densidad de celda constante. Los agentes nucleantes pueden ser gases que producen una solución sobresaturada antes del uso de un PBA, polvos finos que actúan como superficies sólidas para la nucleación celular o agentes espumantes químicos (CBA, que se analiza en el capítulo siguiente). En el caso de los polvos, el agente nucleante permanece térmicamente estable durante el proceso de formación de espuma, mientras que los CBA experimentan una reacción química. Por lo general, los CBA utilizados de esta manera se basan en reacciones endotérmicas, como mezclas de ácido cítrico y bicarbonato de sodio. Los gases son en su mayoría los mismos que los utilizados como PBA e incluyen CO2, N2 y aire. Los polvos pueden ser talco, dióxido de silicio o estearato de calcio, entre otros.
Espuma química
Los agentes espumantes químicos (CBA, también agente espumante químico CFA) son sustancias químicas que reaccionan a altas temperaturas liberando gases que desencadenan el proceso de formación de espuma. Los CBA suelen ser compuestos que contienen más de un elemento. Estos elementos son aceleradores, que controlan la velocidad de reacción, y reguladores celulares, que controlan la estructura celular. La reacción puede ser una descomposición reversible o irreversible, o una reacción entre dos elementos. Para ser utilizados, los CBA deben ser lo suficientemente estables como para no reaccionar en condiciones normales de procesamiento, solo a las temperaturas más altas del proceso. Los CBA suelen ser más costosos que los PBA, por lo que rara vez se utilizan para producir espumas de baja densidad. Aunque el producto químico en sí es caro, los CBA no suelen requerir inversiones en maquinaria de procesamiento como los PBA, y pueden procesarse con casi todas las técnicas de procesamiento de polímeros existentes. Por lo general, son polvos que no necesitan equipo especial de almacenamiento o manipulación, y se pueden agregar simplemente en una tolva o se pueden mezclar fácilmente con el material como masterbatch. También es común usar más de un CBA al mismo tiempo para lograr una estructura requerida, por ejemplo, una mezcla de agentes endotérmicos y exotérmicos.
CBA endotérmicos y exotérmicos
Los CBA se pueden dividir en dos grupos según su calor de reacción. Los CBA endotérmicos absorben el calor mientras se descomponen, mientras que los CBA exotérmicos liberan calor. Esto afecta a la temperatura de fusión solo ligeramente, pero a la reacción en gran medida. La reacción de los CBA exotérmicos es difícil de controlar y, una vez que comienza, es difícil detenerla antes de que todo el agente haya reaccionado. Es por ello que suelen generar más gas y por tanto crean presiones más altas, lo que las hace ideales para procesos de formación de espuma que necesitan la presión pero las estructuras de las células suelen ser heterogéneas. La azodicarbonamida (ADC) es el CBA más utilizado en el mundo. Es exotérmico y se usa solo y en mezclas. Durante la descomposición, libera principalmente N2, pero también CO2, monóxido de carbono y amoníaco. El ADC es un polvo amarillento y produce un residuo blanco o blanquecino durante la descomposición, así como productos sólidos, como biurea y ciamelida, que pueden provocar la aparición de placas. Los CBA endotérmicos producen espumas con tamaños de celda más pequeños, mejores propiedades mecánicas y un procesamiento más controlado. También muestran menos decoloración y se consideran más seguras. En el lado negativo, necesitan más energía para el procesamiento, por lo que requieren tiempos de ciclo más largos. De los CBA endotérmicos, el bicarbonato de sodio es el más utilizado. Es inorgánico, opuesto a orgánico, que son la mayoría de los CBA. Durante la descomposición, produce CO2 y agua, por lo que no se puede utilizar con polímeros que se degradan en presencia de agua.
Elección de un CBA
Al elegir un CBA adecuado para el material y la técnica de procesamiento, se deben tener en cuenta algunos factores. En primer lugar, la temperatura de procesamiento debe ser compatible con la temperatura de reacción del CBA. La reacción debe tener lugar cuando el polímero alcanza la viscosidad adecuada. Los activadores, que reducen la temperatura de reacción, se pueden agregar a un rango de temperatura más amplio. En segundo lugar, la cantidad de gas liberado durante la reacción debe coincidir con la densidad de espuma deseada y el gas en sí debe ser compatible con el material en cuestión. Como se mencionó anteriormente en el capítulo PBA, diferentes gases son más compatibles con diferentes materiales y producen diferentes estructuras celulares. Esta regla se aplica tanto a los convenios colectivos como a los convenios colectivos. Como ADC, algunos CBA producen subproductos que pueden causar degradación en polímeros inadecuados. El subproducto suele ser agua, pero también puede ser amoniaco o gas alcalino o ácido. En tercer lugar, la velocidad de reacción debe coincidir con el proceso y se debe tener en cuenta la influencia del calor de reacción, endotérmico o exotérmico, en el proceso.
Microesferas expandibles
Las microesferas expandibles, también expandibles, son pequeñas esferas de polímero con hidrocarburo en su interior. Cuando se calienta, el polímero se ablanda y aumenta la presión del gas. Si la presión externa es alta, las esferas permanecen pequeñas o solo se expanden ligeramente. Cuando la presión externa cae, como cuando se inyecta material en un molde, las esferas se expanden a un volumen de 40 a 70 veces su volumen no expandido. Se pueden incorporar en extrusión, moldeo por inyección, film soplado, termoformado, rotomoldeo y calandrado. Las microesferas se utilizan a menudo con CBA para formar espuma con una expansión óptima e incluso una estructura celular. Durante el moldeo por inyección, las microesferas no se expanden antes de inyectarse en un molde. La presión dentro del cilindro es demasiado grande y se alivia solo después de la boquilla. Las microesferas expandibles no requieren mucho de la propia máquina de moldeo por inyección. Se prefiere una boquilla con válvula de aguja, una boquilla de cierre, pero no es imprescindible. Su propósito es evitar fugas y caídas de presión dentro del cilindro y así mejorar la reproducibilidad. Si se alcanza la temperatura máxima de las microesferas durante el procesamiento, solo debe ser por un corto tiempo justo antes de la inyección. Se prefiere un tiempo de ciclo corto y el tiempo de enfriamiento se puede reducir en comparación con las piezas sólidas. Si el tiempo de enfriamiento es prolongado, el tornillo no debe llenarse hasta justo antes de la siguiente inyección. Además, la velocidad de inyección debe ser lo suficientemente alta para garantizar un llenado rápido del molde, pero lo suficientemente baja como para no causar demasiado calor por fricción. Aunque los requisitos para la máquina son menores, se exige más de la pieza. La geometría de la pieza no debe ser demasiado compleja y se deben evitar las paredes delgadas. Un espesor de pared inferior a 3 mm no deja suficiente espacio para una expansión suficiente. Si una pieza tiene un espesor de pared variable con secciones de pared delgadas, las secciones de espuma provocan variaciones de densidad diferentes en todo el producto, lo que conduce a propiedades diferentes dentro de la pieza. También puede haber problemas al fabricar piezas grandes, cuando el enfriamiento en el medio puede demorar tanto que las esferas comienzan a colapsar. El espesor máximo varía según el material y la temperatura de procesamiento. En la extrusión, las microesferas se expanden después de haber sido extruidas a través de una matriz. Se exige más de una extrusora que de una máquina de moldeo por inyección. En primer lugar, la relación L/D debe ser 32 o menos. La presión dentro del cilindro evita que las esferas se expandan prematuramente y, por lo tanto, las zonas de vacío o ventilación no se recomiendan y deben taparse si una máquina las tiene. Una ventilación abierta permite que la presión escape y las esferas se expandan, lo que hace que el producto final sea de mala calidad. Al igual que con el moldeo por inyección, durante la extrusión, el tiempo que las esferas están sometidas a altas temperaturas debe mantenerse lo más breve posible. Si el tiempo de residencia es demasiado prolongado, las carcasas comenzarán a deteriorarse y el gas se escapará. Asimismo, la temperatura debe ser más baja en la tolva y más alta justo antes de la matriz. Más importante aún, se debe optimizar la temperatura de la matriz, ya que tiene un efecto mayor sobre la formación de espuma que la temperatura del cilindro. La velocidad de arrastre debe ajustarse a la dimensión de mantenimiento del perfil constante. Es importante tener en cuenta que la resistencia a la fusión del material espumado no es tan grande como la del sólido, por lo que la velocidad no debe aumentarse bruscamente. El enfriamiento se puede mejorar ya que detiene el crecimiento celular y, por lo tanto, el enfriamiento rápido le da al perfil una superficie más suave. Si se necesita una superficie aún más lisa, se debe coextruir una capa de superficie sólida.